Tüpraş integrates robots to advance digitalization of Turkish refineries
As part of Türkiye Petrol Rafinerileri AS’s (Tüpraş) digitalization transformation plan, the operator in 2021-22 began pilot tests using artificial intelligence (AI)-supported autonomous robot applications at its Turkish refineries.
First commissioned at the 11.3-million tonne/year (tpy) Izmit refinery in District Körfez of Turkey’s northwestern Kocaeli province, and subsequently at the 5.4-million tpy refinery in Kırıkkale province, the trial studies involved deployment of Boston Dynamics Inc.’s Spot, a four-legged autonomous mobile robot equipped with the Cognite Data Fusion (CDF) data platform from software partner Cognite. Following favorable trial runs of the robot at both refineries, Tüpraş is now evaluating use of the integrated robotic technology at other production sites.
In addition to discussing Tüpras’s broader digitalization strategy, this article provides an overview of the rationale behind, digital technologies involved in, and preliminary results of Spot’s field testing at the Turkish refineries.
Spot’s deployment in Tüpras refineries follows previous testing of the CDF-enabled robot by Aker BP ASA and bp PLC on their respective offshore production platforms in the North Sea and Gulf of Mexico (OGJ, Mar. 7, 2022, p. 26).
Digital transformation
Intensified in 2020-21 following outbreak of the global pandemic and the operator’s commitment to achieve carbon neutrality by 2050, Tüpraş’s digitalization plan focuses on implementing digital technologies based on an interconnectedness that enables the company’s workforce to adapt more rapidly to changing work conditions and access the real-time data required for decision making. These strategies are aimed at directly supporting the company’s main goals of operational excellence, efficiency, sustainability, physical safety, cybersecurity, and operational transparency.
Within the framework of the developed strategies, digitalization initiatives target all applications involving managing production processes as well as more analytical, data-based activities. The latter include implementing tools such as mobile and wearable technologies, robotics, and applications and software involved in process optimization, predictive maintenance, crude oil supply, production planning, and market-price forecasting, among other areas.
The operator said a primary goal of digitalization for its refineries has been to create smart, autonomous, risk-free refining operations by employing solutions that will increase efficiency in all occupational safety and production processes, including maintenance. Areas of particular focus in this regard include:
- Ensuring field observation and routine work is autonomous by using robotic processes.
- Providing remote operation and equipment management.
- Using virtual technologies in occupational safety and emergency management trainings and field tours.
- Providing net-zero and maximum energy efficiency with digitalization and AI.
- Developing a system to monitor continuous improvement via autonomous refinery processes and smart devices.
- Establishing a smart, integrated inventory stock management system.
- Implementing digital maintenance processes.
- Introducing systematic equipment-health and asset monitoring management.
- Activating AI-supported process controls.
- Modernizing financial systems.
- Providing security and quality management in software development processes.
- Ensuring process optimization by providing inter-application integrity across platforms.
Robotics studies
To execute its digital strategy’s robotics roadmap, Tüpraş in 2020 established a robotics team dedicated to developing projects that, based on a safety-first principle, could be considered for implementation at its refineries. Following previous pilot trials of robotic technologies in periodical control studies at refinery oil storage tanks, the robotics team—with contributions from applicable technical teams at the Izmit and Kirikkale refineries—undertook a project in 2021 to determine necessary parameters for testing AI-supported autonomous robot applications in the high-risk working environments of the manufacturing plants.
Robot trials, capabilities
The Tüpras, robotics team deployed Spot consecutively at the Izmit and Kirikkale refineries in 2021, with both pilot programs concluded by early 2022.
Intended to support a safer working environment at the production sites, Spot was selected initially for its ability to execute repetitive works associated with higher-risk processes and enable technical teams at the refineries to instead focus their specialized skills elsewhere within the plants (Fig.1).
Outfitted with a variety of AI-powered mechanical capabilities and the integrated CDF platform, Spot’s deployment during trial runs at the refineries yielded a series of operational benefits, Tüpraş said.
Capable of detecting obstacles on its preprogrammed routes using its surrounding detection sensors, the robot was able to determine actions to be taken to overcome such impediments using its internal decision-support mechanisms, without requiring intervention from refinery personnel (Fig. 2).
Additional capabilities of the AI-supported robot included:
- Autonomous operation. The CDF platform—supported by 3D models—allowed easy programming and defining of desired actions, as well as predictable outcomes. After receiving necessary instructions, the robot was able to work alone and complete its tasks without requiring any additional direction. Supported with a wireless connection, the robot also was able to provide any required data to support the operator, including transmitting live images in real-time using its 360° camera. The robot also allowed for remote manual control to manage non-routine and unplanned operational needs.
- Analog data. Alongside its ability to autonomously perform readings of various meters, level indicators, valve opening indicators, temperatures, and other safety controls at the sites, the robot allowed images to be retrieved from its photos of equipment, which were subsequently processed to create digital data that was recorded to create a trackable time series (Fig. 3).
- Leak detection. The robot’s AI-supported cameras allowed for easy detection of any water or steam leaks around units, while built-in sensors detected any ambient gas leaks in the surrounding environment.
- Thermal imaging. A thermal camera on the robot allowed Spot to report temperature values for requested areas within the refineries. These temperature data could then be processed and compared with historical data via the CDFplatform to create or identify more intelligent warning systems for operators.
- 3D modeling. The robot was able to create 3D modeling of its surrounding environment with its scanning cameras. Objects detected in the 3D models could then be processed as images and compared with previously retrieved data to create a warning for any unidentified object that should not be in a particular location. This allowed for ensuring that evacuation routes required for use in case of an emergency were always kept clear.
Next steps
Following the robot’s trial runs at the refineries, Tüpraş said in 2022 that it will be performing feasibility studies at other sites for implementation of Spot once it completes a more detailed evaluation of data and information collected during the Izmit and Kirikkale field tests.
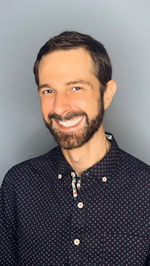
Robert Brelsford | Downstream Editor
Robert Brelsford joined Oil & Gas Journal in October 2013 as downstream technology editor after 8 years as a crude oil price and news reporter on spot crude transactions at the US Gulf Coast, West Coast, Canadian, and Latin American markets. He holds a BA (2000) in English from Rice University and an MS (2003) in education and social policy from Northwestern University.