Optimized acid fracturing increases North Sea production
ConocoPhillips Co. (COP) comprehensively reviewed stimulation techniques and acid fracturing designs in North Sea chalks to improve its stimulation designs. The choice between matrix acidization, acid fracturing, and proppant fracturing depended upon field economics and formation characteristics, and extensive laboratory testing, coupled with reservoir simulations, aided in determining the best technique for the reservoir.
For acid fracturing, COP evolved best practices from 2016 to 2024 by rigorously history-matching treatment data and reviewing production performance. Improvements in acid and pad stage volume and numbers, chemical compatibility, crosslinker type, and sleeve-ball designs led to increased long-term production, improved fracture treatments, and decreased operational failures.
Stimulation selection
COP’s study of stimulation techniques for North Sea chalk fields included matrix acidization, acid fracturing, and proppant fracturing. Field economics was the primary consideration in determining stimulation method, and the productivity of the stimulation depended on the type of chalk encountered.
Stimulation selection considered the formation permeability, porosity, rock embedment strength (RES), and acid solubility. Solubility determined the formation’s response to acid, permeability and porosity guided the type and size of stimulation required for economic productivity, and RES determined whether the fracture would remain productive after stimulation.
Acid solubility also drove acid fracture vs. proppant fracture decisions. A proposed 72% minimum acid solubility cutoff came from an average of North Sea chalk and carbonate formation solubility measurements, which had a 65-85% acid solubility range. Results from Valdemar’s chalk stimulations, however, showed poor productivity from acid fracturing within this solubility range. Proppant stimulations performed better at Valdemar, indicating that acid solubility represented only one parameter to achieve good stimulation results. COP outlined additional laboratory testing procedures to determine the best stimulation for each type of chalk formation.
Acid solubility and acid reaction rate tests (via rotating disk) determined formation acid dissolution, and gel testing, core acid-etching, and fracture conductivity tests determined fracture conductivity.
For acid fracturing treatments, the non-acid gelled pad generates fracture geometry. The gel, therefore, was tested to ensure its compatibility with formation temperatures and acid formulations in the acid pad. Gal testing was also required for leakoff into the formation, shear recovery, blockage of acid-induced wormholes to maintain acid penetration into the fracture, shear rate dependent viscosity, internal breaker effectiveness, and breaker time to reduce gel viscosity after the treatment for effective flowback.
Proppant stimulation provides a good alternative to acid fracturing when the formation does not respond well to acid fracturing, either through poor acid solubility, poor initial fracture conductivity after the acid frac, or poor fracture conductivity after depletion, which increases skin over time. In the Valdemar case, for example, having enough lowerporosity, low-calcite content chalk in the formation prevented effective acid treatments. Tip screenout proppant fracturing also provides solids control in reservoirs which have a history of producing chalk. RES also helps guide decisions on proppant fracturing vs. acid fracturing.
"The revised treatments reduced premature acid spending in the first stage, achieved CFA at the third stage, and ultimately required shorter pumping times and less chemicals.”
COP defines RES as the force required to penetrate a 0.05-in. diameter steel ball 0.00625 in. into a formation sample. High RES rocks maintain initial fracture conductivity under high net-stress loads or under high depletion and do not require proppant to maintain conductivity.
The fractured rock face’s natural asperities, etched surfaces, and wormholes provide conductivity. Low RES formations, by contrast, close acid-etched fractures under high loads until little conductivity remains. These formations require proppant treatment. Effective
acid fracturing requires a minimum 20,000-psi RES cutoff, but most North Sea chalks have high porosity (35-45%) which results in low RES.
Proppant fracture half lengths tend to be significantly longer than acid fracture half lengths, extending 500-1,000 ft compared with about 90 ft for industry-average acid fractures and 225 ft for COP-optimized acid fractures. Longer half lengths typically improve production and the well’s ultimate recovery, but frac hits with nearby wells must be avoided (Fig. 1).
High porosity chalks respond well to high-rate matrix acidizing without fracturing. In low porosity and layered intervals, acid will preferentially divert through higher porosity or higher permeability layers, leaving the bulk of the formation unstimulated.
In these circumstances, and for low permeability reservoirs (K < 1 md), acid fracturing is the preferred technique for stimulation.
Optimized acid fracturing An extensive review of acid-etched fractures in Ekofisk Paleocene reservoirs revealed incremental treatment improvements from 2016 to the present. Treatment optimization variables included pad acid volumes, injection rates, acid concentration and exposure time, pad- and acid-stage cycling, gel type, and gel loading.
More than 600 stages of treatment provided a database for acid-fracturing improvements in carbonates. For Ekofisk completions, post-2017 optimized stimulations used smaller pads and acid volumes than original 2016 completions. The original larger treatments did not yield higher fracture conductivity or well performance, and smaller treatments were more economical. Additionally, the larger treatments risked communicating through fractures with offset wells.
These revised designs, however, required rigorous treatment modeling coupled with 3D reservoir simulation for optimal fracture placement. Stages also required monitoring for acid dissolution using real time formation-face pressure analysis to avoid pumping acid after the acid-carbonate reaction reached equilibrium.
Another hinderance to productivity came from incompatibility of surfactants with the crosslinker in the 50 lb/thousand gal titanate crosslinked fracture gel. A change to a 35 lb/thousand gal borate crosslinked gel and a reduction in friction reducer concentration eliminated fluid incompatibility and produced a gel with lower shear sensitivity for more robustness during the treatment.
Eldfisk completions required both 15% and 28% HCl concentrations, though most treatments used 15% HCl. The higher 28% HCl concentration is generally not recommended except in circumstances of high reservoir pressure, high fracture gradients, low pump rates, and low leakoff. Gelled acid yielded no benefits, leading to the exclusive use of neat acid.
High Ekofisk formation temperatures (about 250° F.) result in short exposure times of about 6-7 min for 15% HCl and 4 min for 28% HCl. Additional exposure risks excessive rock dissolution, especially for uninhibited acids. When this happens, fracture pressure falls below closure stress, resulting in a closed fracture early in the treatment.
Successful jobs maintain fractures throughout treatment stages until the end of the job, when fracture closing results in stimulation of the near wellbore region. This closed fracture acidizing (CFA) stage improves near-wellbore fluid flow through channel-type features and wormholing. Excessive near-wellbore chalk dissolution, however, may compromise liner integrity. Typical practice tails in 28% HCl at the end of the job to enhance this final stimulation stage.
Preliminary stage acid volumes determined exposure times, and treatments included viscous pad stages alternating among acid stages to minimize loss of fracture pressure and keep fractures open. Based on multiple well analyses from ca. 2017 completions, revised treatments eliminated a fourth pad and acid cycle in the standard treatments because pressure analysis showed that the last cycle only produced CFA. The revised treatments reduced premature acid spending in the first stage, achieved CFA at the third stage, and ultimately required shorter pumping times and less chemicals (Fig. 2). Long-term production analysis showed no degradation compared with the previous four-stage treatments.
Leakoff control through fluid-loss additives (FLA) added to completions in 2018 prevented spending through non-productive cavities or wormholes. FLAs are fine dissolvable particles added to the second and third pad stages. They maintain an effective pressure front to extend the fracture. Field response from FLA showed a continuous increase in pressure when the FLA landed on bottom (Fig. 3). Long-term production analysis yielded 525 md-ft fracture conductivity. Pre-2018 completions typically resulted in 55-330 md-ft fracture conductivities, indicating that FLA extended the fractures until the final pad.
A treatment pumped in 2018 with these revised schedules, optimized gelled pad, and 28% HCl acid volumes in Eldfisk targeting the Hod formation showed significant improvement over pre-2018 practices (the higher acid concentration counteracted the low acid spending characteristics of this formation). A 3-year production history match yielded 750 md-ft bulk acid etched conductivity compared with 105 md-ft calculated from a similar match for a well completed in 2016. Dimensionless fracture conductivity (FcD) calculations yielded FcD = 7.0 for the 2018 optimized treatment compared with 4.0 for pre-2017 treated wells.
The long-term production successes on wells stimulated post-2018 using these design changes allowed the operator to focus on lower completion equipment optimization and reduced overall well costs.
Lower completion optimization
Fig. 4 shows a typical Greater Ekofisk sliding sleeve completion with heavy-weight 23.2 lb/ft, 5-in. liner through the reservoir and 5.5-in. x 4.4-in. tubing in the upper completion. The table summarizes generational lower completion optimizations from 2015-23. These optimizations increased completion length, minimized well interventions, provided conformance control, and enabled limited entry pressure tuning.
The fracture design determined the number of stages in the well, and a limited entry design determined the number of ball-activated sleeves in a stage, which are analogous to clusters in perforated completions. Ball-activated sliding sleeves and pressure-actuated toe valves required no interventions for opening. These sleeves can also be shifted with intervention post-completion for water shutoff. Limited entry targeted a minimum 1,000-psi differential pressure across the sleeve.
Sleeve placement required an initial estimate of stimulation stages and sleeves for each stage. This estimate, in turn, was based on pore pressure and log-derived permeability profiles across the stage, formation breakdown pressure, limited entry differential pressure across the sleeves, and the maximum surface treating pressure. Generation 3 and 4 designs used different nozzle sizes in the sliding sleeves to maintain limited entry and extend the number of clusters in the stage. Production results guided design revisions in an iterative trial-and-error process.
Generations 1-4 used ⅛-in. increment sleeves, limiting the number of stimulation stages to seven. The limit comes from the ball-seal design. Balls seal against profiles to shift sleeves and isolate zones during acid stimulation stages. The cement wiper-dart size and minimum inner diameter of the upper completion limits the largest ball size and therefore total number of balls that can be pumped for ⅛-in. incremental sleeve seats. The ideal number of sleeves in the cluster, however, depends on the formation characteristics and reservoir simulations. The ⅛-in. increment sleeves, therefore, may result in less stages than ideally required.
Generation 5 implemented a minimum 2.5% ball-ball seat overlap which increased the number of sleeves in a stage up to practical completion space-out limits. The small overlap was tested to ensure that the balls held expected differential pressure during the stimulation treatment, including limited entry backpressure.
Early generation designs used degradable polymeric balls, but these were replaced with either degradable metallic balls or acid-resistant degradable metallic balls based on high sleeve-opening failure rates associated with polymeric balls. The metallic balls degrade through galvanic corrosion but are susceptible to acid and can leak during acid treatments. Acid-resistant degradable balls, therefore, were tried to provide reliable seating during the acid job but degrade after the treatment.
The ball change reduced sleeve opening failures to 8-9% from 13% (red relative to green counts in Fig. 5). Zonal isolation, however, failed more often, with 41% failure using polymeric balls relative to 32-35% with metallic balls. The acid-resistant balls did not provide a significant advantage over standard metallic balls. Zonal isolation failure was addressed by dropping multiple balls for backup, but Fig. 5 shows that too many failures still occurred even with multiple ball drops. These failures are the subject of ongoing research.
Despite the ball failures, the unlimited frac sleeves performed as designed, and the system provided longer completions without compromising sleeve spacing or pump rate.
Based on “Acid Fracturing Treatment Design Optimization in North Sea Chalk Wells in Norway,” SPE-223572-MS, SPE Hydraulic Fracturing Technology Conference and Exhibition, The Woodlands, Tex., Feb. 4 – 6, 2025, and “Completion and Stimulation Design Evolution in Tight Chalk Formations in Offshore Norway,” SPE-223572-MS, SPE Journal, Feb 2025.
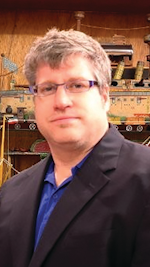
Alex Procyk | Upstream Editor
Alex Procyk is Upstream Editor at Oil & Gas Journal. He has also served as a principal technical professional at Halliburton and as a completion engineer at ConocoPhillips. He holds a BS in chemistry (1987) from Kent State University and a PhD in chemistry (1992) from Carnegie Mellon University. He is a member of the Society of Petroleum Engineers (SPE).