Fracturing emissions cut with next generation techniques
Adopting next-generation pump power, wet sand, and dry chemicals reduces fracturing emissions by about 30%. SLB conducted a lifecycle assessment of emissions from typical US fracturing operations. The study quantified the CO2 equivalent (CO2e) footprint from all aspects of the operations including material sources, fuel consumption while mobilizing equipment to location, fracturing, and post-fracturing operations.
Results showed that pumping the fracturing treatment produced about a third of total emissions, with flaring and equipment mobilization-demobilization contributing about 25%.
Emissions analysis
Published data from North American fracturing treatments provided input parameters for US fracturing emission analysis. Table 1 lists fracturing treatment parameters obtained from Rystad Energy, IHS Markit, and FracFocus sources. Data were obtained from pads containing four wells with 10,000-ft average lateral lengths and 20,000-lb proppant/well.
Water and proppant account for more than 98% of the mass of the fracturing fluid with chemicals accounting for the other 2%. The analysis only included sand, excluding ceramic proppants which have a more energy-intensive manufacturing process. Sand production includes mining, washing, sorting, and drying.
Wet sand was considered in the analysis. Wet sand skips the drying process and is sourced locally to the frac pad, minimizing emissions (OGJ, Jul. 5, 2021, pp. 42-47). Sand moisture content is 1-10% by weight and increases transport emissions. This additional component was included in the wet sand analysis.
Friction reducers (FR), surfactants, clay stabilizers, iron controllers, and breakers comprise the chemical packages, with FR accounting for most of the volume. Emission factors for these additives came from carbon accounting databases.
Water sourcing and conditioning were not considered in the analysis. Likewise, the carbon intensity for manufacturing isolation plugs and intervention-related material was not included.
Logistics
Emissions from logistics included transportation for water, chemicals, proppant, fleet equipment, and pumping crews. Fig. 1 shows average distances from the wellsite for these components.
A 75-mile radius represented the average proppant transport distance, and this distance was also used for chemical transport. Water transport significantly varies by location through pipelines and trucking, but SLB used a generic 10-mile transfer system with 0.5-mile transfer pump spacing and 0.027-gal diesel/1,000-gal water fuel consumption.
In Haynesville, Permian basin, and Midland basin, equipment travels from 50-150 miles to location, and an average of 100 miles was used for analysis, with crew camps placed 15 miles away due to nearby accommodations.
SLB adopted a 10.18-kg CO2e/gal combusted diesel fuel CO2e logistics emission factor based on EPA guidelines. Trucks were assumed to be more than 33,001 lb in weight with mileage estimates applied from the EPA’s physical emissions rate estimator (PERE) and Smart Way programs. Mobilized equipment included 25 high-pressure pumps, five fracturing tanks, one fracturing van, one blender, and one hydration unit in addition to a flatbed for iron and low-pressure hoses.
Fracturing service
Table 2 lists fuel consumption for key equipment during fracturing operations. The emission calculations also accounted for the fracturing van, additive pumps, transfer pumps, and batch mixer. Tier 2 diesel reciprocating engines powered the pumps. Standard diesel-powered pumps run for 1 hour 40 min per stage with 20-min idle time between stages. Although 25 pumps were included in the mobilization scheme, only 20 were assumed to run at any one time with five held for contingencies.
Flaring
Flaring represents the highest emissions-intensive post-fracturing cleanup activity. Flaring from post-fracturing treatments was not explicitly included in Rystad Energy’s analysis, therefore SLB estimated post-fracture cleanup flaring volumes based on a 1.0-MMscfd average first-year cumulative production rate with a 15-day post fracture flaring duration.
Emission calculations assumed a simplified 85% methane, 10% ethane, and 5% propane gas composition. Table 3 lists regional flaring efficiencies expressed as destructive removal efficiency (DRE). An average DRE of 91% was assumed for the study based on data from Eagle Ford, Bakken, and Permian basins. An oil production greenhouse gas emissions estimator (OPGEE) provided production emission estimates using a 25 global warming potential (GWP) factor for methane and a 3.1 GWP factor for volatile organic compounds. GWP measures the emission energy 1 ton of a gas will absorb over 100 years relative to the emission of 1 ton of CO2. A larger GWP warms the Earth more than CO2 over this period.
Produced water disposal
Produced water estimates assumed 1.6 million bbl of water injection into four wells with 47% water flowback per EPA data, resulting in 188,000 bbl of produced water/well. Produced water treatment schemes generally consist of a crossflow scrubber for primary oil separation and a depurator for secondary separation by floatation. Only the motors running the depurator were considered in the greenhouse gas calculations for water treatment. Total emissions from these motors were 376-kg CO2e for four wells.
Transport of treated produced water 1 km to a central water treatment plant requires an estimated 328 trucking trips, each transporting 143 bbl of water. Emissions from these trucks, using gasoline as fuel, totaled 1,000-kg CO2e.
Holistic emission estimates
Total emissions from all fracturing and related operations combine to nearly 13,000 tonnes (Table 4). Fig. 2 shows the breakdown of emissions per operation. Wellsite execution comprises most emissions (33%) followed by flaring (26%), and proppant and equipment mobilization-demobilization (26%). These trends generally hold for most fracturing operations, though actual percentages will vary depending on site specific circumstances. For example, SLB determined that wet sand reduces the proppant manufacturing component by 1,089 tonnes CO2e, and substituting green eluent burners in flares improves combustion efficiency by more than 99.8%.
Substituting dry FR in the analysis reduces emissions from transportation. Liquid FR contains 20-30% active polyacrylamide compared with 90% in dry FR. The base case for this study required about 74,000 gal of FR which resulted in 15 deliveries over the 75-mile transport route. Dry FR requires only eight deliveries, reducing emissions from FR by 46%.
Among wellsite pumping operations, the high-pressure pumps produced 88% of total equipment emissions. This component accounts for 29% of the holistic fracturing service emissions. Given this large contribution, SLB performed a detailed study into alternative high-pressure pump power.
Pump power alternatives
Alternative pump power includes turbine direct drive, gas mechanical, and electric. Turbine direct drive units use a turbine to power pumps, air filtration, and lubrication systems. Gas mechanical units comprise reciprocating engines powered by natural gas, which can be supplied from field gas (OGJ, Jan. 9, 2021, pp. 32-35). These engines have higher thermal efficiency than other power sources. Both systems directly connect to the pumps and ancillary equipment.
Electric drive units require external electricity generation sources, and their emissions depend upon the type of source supplying the power. Few frac spreads are powered by the grid, and tracking their emissions would have to go through the plant producing the bulk of electricity serving that region. Most, instead, have wellsite mobile power units supplying electricity from generators driven by turbine or reciprocating engines powered by natural gas. SLB assumed that emissions from these sources were on average 30% less than those produced from Tier 2 diesels. Tier 4 diesels are expected to have similar emission reduction from Tier 2 sources.
Dual fuel options for efficiently running frac spreads also have emission impacts. Dual fuel engines have additional controls for a gas train to switch from diesel to natural gas. For Tier 2 engines, gas substitution is typically about 40%. Tier 4 engines run with higher substitution. Although natural gas has lower CO2e emissions compared with diesel, methane slip occurs in these engines resulting in unburned methane releases.
SLB analyzed dual-fuel cases with 85%, 65%, and 35% gas for Tier 2 and Tier 4 diesels with and without methane slip. Tier 4 diesels showed little impact of methane slip on emissions, but Tier 2 engines generally produced 15-34% more emissions under slippage based on 35% and 85% gas substitution, respectively.
Idle reduction technology (IRT) using stop-start systems minimizes emissions during downtime between fracturing stages when pumps are traditionally left to idle. SLB studied a battery-electric starter start-stop scheme to reduce idle time by 50%. Reducing idle time to 10 min from 20 min saves about 43 tonnes of CO2e from the total emission estimate.
Alternative analysis
Emission estimates combining proppant, chemical, and next generation power alternatives are shown in Fig. 3. Scenario 1 shows total emissions using wet sand, electric pumps, start-stop technology, high-efficiency burners, and post-fracturing well shut in to reduce water production and therefore flaring. Scenario 2 shows the total emissions when Tier-4 dual fuel pumps with 65% gas usage replace electric pumps. The scenarios achieved 35% and 28% emissions reduction, respectively.
Based on “A Comprehensive Life Cycle Assessment of Hydraulic Fracturing,” SE-220480-MS, SPE International Health, Safety, Environment and Sustainability Conference and Exhibition, Abu Dhabi, UAE, Sept. 10-12, 2024.
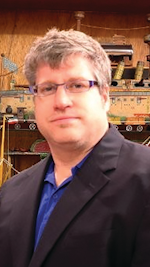
Alex Procyk | Upstream Editor
Alex Procyk is Upstream Editor at Oil & Gas Journal. He has also served as a principal technical professional at Halliburton and as a completion engineer at ConocoPhillips. He holds a BS in chemistry (1987) from Kent State University and a PhD in chemistry (1992) from Carnegie Mellon University. He is a member of the Society of Petroleum Engineers (SPE).