Nigerian grassroots integrated complex to start first-half 2023
Nigerian conglomerate Dangote Industries Ltd. (Dangote Group) subsidiary Dangote Oil Refining Co. (DORC) is nearing startup of its long-planned grassroots integrated refining and petrochemical complex in southwestern Nigeria’s Lekki Free Trade Zone, in Ibeju-Lekki, Lagos (OGJ Online, Nov. 6, 2019).
Recently completing major construction activities and now with Nigeria’s federal government an official stakeholder, the integrated complex—which will become the world’s largest single-train refinery upon startup—is slated for full commissioning in early 2023.
Long-term refined products demand growth in West Africa has prompted many nations in the region to advance plans for expanding refining capacity through a series of newly commissioned and recently announced projects involving modernization of existing refineries as well as construction of new manufacturing sites.
Alongside examining the status of the refinery and Nigeria’s latest decision to formally participate in the project, this article presents an overview of units and process technologies that will be featured at the soon-to-be operating integrated complex.
Test runs, startup activities
In late-October 2022, DORC confirmed to Nigerian local media that it had achieved 100% mechanical completion of the Lekki integrated complex, including a refinery equipped to process 650,000 b/d of Nigerian crude oil and interconnected downstream units to help Nigeria meet domestic demand for finished petroleum products, create surplus products and chemicals for export, and eliminate the need for costly imports from abroad.
Previously slated for commissioning in third-quarter 2022 and with construction only recently completed, DORC is executing test runs of major units and equipment at the mega-refinery ahead of its revised start of official commercial production now scheduled for first-half 2023, according to the operator and government officials.
Federal investment
In early August 2021, the Nigerian government’s federal executive council (FEC), led by President Muhammadu Buhari, approved state-owned NNPC Ltd. (formerly Nigerian National Petroleum Co.) to invest $2.76 billion for acquisition of a 20% equity interest in the privately held DORC integrated complex. The acquisition was part of expanded efforts to further ensure Nigeria’s future energy independence, Mele Kyari, NNPC’s managing director and chief executive officer, said in a series of press statements, government speeches, and local Nigerian live broadcasts.
The DORC investment joins a series of other ongoing projects being conducted by the Nigerian government to modernize and expand capacities of NNPC’s aging four main refineries under a broader national program that seeks to meet Nigeria’s domestic demand for refined products and eliminate its current reliance on foreign imports (OGJ, Jan. 4, 2021, p. 51).
According to Kyari, the government’s rationale for investing in DORC stemmed from the fact that the refinery is under no obligation to purchase Nigerian crude as feedstock. Securing ownership interest in the refinery allows NNPC to have a voice in where the refinery sources its feedstock, as well as ensuring the state-owned oil company has a ready outlet for its own Nigerian crude production.
Formal acquisition of interest in DORC followed the federal government’s 2019 commitment to support the refinery via supply of crude feedstock and other necessary but unidentified feeds (OGJ Online, Nov. 6, 2019).
On multiple occasions, the government has said it expects startup of DORC’s complex combined with NNPC’s continued investments in rehabilitating its own refiners and construction of smaller, privately owned modular refineries will not only more than satisfy domestic product demand but provide surplus production to transform the currently import-dependent West African nation into a major exporter of products to other destinations within and beyond the African continent.
According to government releases in 2022, DORC’s refinery—which is configured to process a variety of African crudes, some Middle Eastern grades, and US light tight oil—will be able to produce 33 million tpy of petroleum products, including up to about 10.5 million tpy combined of Euro 5-quality gasoline and diesel, 4 million tpy of Jet A-1 aviation fuel, as well as kerosine, LPG, and petrochemicals such as polypropylene. In April 2022, DORC informed local Nigerian media that 40% of the refinery’s overall production will be enough to meet Nigeria’s entire in-country product demand, leaving 60% of output from the complex available for export markets.
Once fully operating, the complex—which employs more than 30,000 local and contracted employees—will more than double Nigeria’s the total production capacity from NNPC’s yet-to-be-fully-rehabilitated refineries, allowing the country to save an estimated $50 billion/year on importing oil products from abroad, the government said.
Refinery units, technologies
Previously projected to require a total capital investment of $12 billion to complete, the now $19.5-20-billion Lekki complex houses several major installations that, in addition to the site’s main refining plant, include a 3.6-million tpy polypropylene plant, a 3-million tpy urea plant, and gas processing installations to accommodate 3 bcfd of natural gas that will be transported through 1,100 km of subsea pipeline (Figs. 2-4).
Associated infrastructure at the site consists of a single-point mooring terminal connected to the refinery for crude oil and product handling. The refinery also is equipped with a dedicated steam-and-power generation system.
Alongside the refinery’s main combined crude-vacuum distillation unit (CVDU), the refining plant includes a single-train residue fluid catalytic cracking (RFCC) unit, mild hydrocracker, alkylation unit, naphtha hydrofining unit, and continuous catalytic reforming (CCR) units for production of gasoline and diesel. The plant also is equipped with a captive power plant and dedicated steam-and-power generation, including standby units to ensure uninterrupted power supply. The refinery also has its own wastewater treatment system featuring separate plants for:
- Effluent treatment.
- Reverse osmosis, demineralization, and condensed polishing.
- Raw-water intake.
- Raw-water treatment.
Implemented by Engineers India Ltd. (EIL)—which serves as project management consultant and delivered engineering, procurement, and construction management of the project—the refinery is outfitted with a selection of process technologies aimed at ensuring production complies with Euro 5 specifications.
Honeywell UOP LLC delivered technology licensing, design services, and critical equipment for several processing units, including its proprietary:
- UOP RFCC process for producing transportation fuels and propylene.
- CCR Platforming process for producing high-octane gasoline blending components.
- Unicracking process for diesel production.
- Penex process for producing high-octane gasoline.
Alongside proprietary catalyst regeneration and dryer regeneration control systems, high-performance column trays, and heat exchanger tubes, UOP’s equipment delivery included a modular CCR unit, catalyst coolers, a third-stage separator system for the RFCC unit, and two pressure-swing adsorption (PSA) units.
DuPont Clean Technologies supplied its proprietary technology licensing, design, and equipment for a 27,000-b/sd STRATCO alkylation unit and 260-tonne/day MECS sulfuric acid regeneration unit, both of which enable the refinery to produce high-octane, low-sulfur, low-RVP, zero-olefins alkylate. DuPont also provided licensing, design, and equipment for its proprietary MECS DynaWave tail gas scrubbing and BELCO EDV stack scrubbing units to help the refinery meet gasoline-pool octane and emissions requirements. Designed to meet global standards for particulate matter and SOx emissions, the DynaWave wet-gas scrubber ensures full-time compliance with emissions regulations on both of the refinery’s 115-tonne/day sulfur recovery units (SRU). The BELCO EDV also provides a purge treatment to condition the scrubber effluent.
Air Liquide SA supplied two hydrogen production steam methane reformer (SMR) units for the refinery’s hydrogen-generation complex, which produces 200,000 normal cu m/hr of hydrogen and high-quality steam for the refining plant.
Schneider Electric Industries SAS supplied DORC with a suite of four of its process automation systems and software, all of which are used to drive supply chain and operational efficiency and enhance reliability of the new refinery by mitigating safety hazards and preventing unscheduled shutdowns. Schneider Electric’s delivery included the following proprietary systems and software:
- EcoStruxure Foxboro distributed control system, an IoT-enabled, open-and-interoperable system architecture and platform enabling scalable design and operation of the refinery’s connected systems with cybersecurity built in across connected products, edge control and apps, analytics, and services.
- Triconex process safety systems and solutions, including emergency shutdown systems, to maximize safety and efficiency of operations and to improve reliability of equipment assets.
- PIONIR analytical fuels-blending systems, including process analyzers, to improve process optimization, asset protection, and compliance with environmental regulations by providing reliable, real-time measurement of hydrocarbon streams.
- SimSci and Wonderware software, including unified supply chain management and operations management software, to unify planning and scheduling, as well as improve real-time data collection and analysis for further optimizing operations and product blending.
After using Aspen Technology Inc.’s Aspen PIMS-AO software to help select configuration, critical design, and expansion studies for the refinery during the planning phase, DORC will again use PIMS-AO following the refinery’s full startup to streamline feedstock selection, product-slate optimization, and production planning, as well as to report refining economics and to determine ongoing product-slate and feedstock selection.
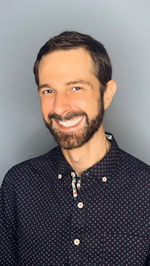
Robert Brelsford | Downstream Editor
Robert Brelsford joined Oil & Gas Journal in October 2013 as downstream technology editor after 8 years as a crude oil price and news reporter on spot crude transactions at the US Gulf Coast, West Coast, Canadian, and Latin American markets. He holds a BA (2000) in English from Rice University and an MS (2003) in education and social policy from Northwestern University.