US petrochemical operators resume major projects, pause future plans
As industry slowly began its recovery in first-half 2021 amid ongoing coronavirus (COVID-19) vaccine rollouts and steady demand for chemical-based materials used to produce hygiene-related products, operators resumed construction in earnest on several major US petrochemical projects that, nearing prepandemic completion, were delayed following the 2020 viral outbreak.
Despite sustained healthy demand for chemical products and currently ample supplies of ethane feedstock, however, other petrochemical producers deferred further development of previously announced US projects. Alongside lingering uncertainty about potential market impacts that could arise from still-emerging COVID-19 variants, operators also remained unclear regarding the effects anticipated startup of domestic and international capacity additions through 2022 could have on secure access to cheaper feedstock supplies sourced from North American shale production.
In addition to providing an update on the status of major US petrochemical projects nearing startup and recently commissioned, this article examines a selection of newly announced projects under active development and those still facing delays.
Major projects advance
Before the early 2020 COVID-19 outbreak and subsequent pandemic-related lockdowns, construction was well under way on three new US ethane crackers.
Following slowdowns in mid-March 2020 and January 2021 caused by threats of the spreading COVID-19 virus, Royal Dutch Shell PLC resumed full construction activities in first-half 2021 on subsidiary Shell Chemical Appalachia LLC’s Shell Polymers Monaca site, which includes a dual 1.5-million tonne/year (tpy) ethylene and 1.6-million tpy polyethylene complex under development just southwest of Monaca, Pa., along the Ohio River in Potter and Center Townships, Beaver County, 30 miles northwest of Pittsburgh (OGJ, Aug. 3, 2020, p. 35).
Fig. 1 shows operations underway at the Shell Polymers Monaca complex during the early morning hours of July 9, 2021.
While Shell has yet to officially confirm any definitive timeline for startup of the Appalachian petrochemical complex, an updated economic impact analysis (EIA) of the project finalized by Robert Morris University professors in April 2021 and made publicly available on July 14 indicated the Shell Polymers Monaca complex is scheduled to be completed and operational by 2022 pending absence of any state-ordered shutdowns or additional pandemic-related delays.
Commissioned by Shell but conducted without the operator’s direct participation, the independent EIA study estimated overall cost of the project—for which Shell is receiving about $1.7 billion in Pennsylvania state corporate tax credits—has increased to at least $10 billion from its 2014 original price tag of $6 billion.
Midyear release of the updated EIA follows the Pennsylvania Department of Environmental Protection’s (DEP) February 2021 approval of modified air quality plans for which Shell Chemical Appalachia applied in December 2019 and February 2020 to request authorization for as-built changes in design and construction of the Shell Polymers Monaca site. Proposed changes included minor equipment additions, removal and downsizing of permitted equipment, as well as increases and decreases in capacities of pumping, incineration, blending, heating, storage, loading, water circulation, and flaring equipment, DEP said.
Designed to produce ethylene, high-density polyethylene (HDPE), and linear low-density polyethylene (LLDPE) from nearby supplies of low-cost Marcellus and Utica shale ethane, Shell’s Appalachian petrochemical complex will include seven tail gas and natural gas-fired ethane cracking furnaces with a heat input rating of 620 MMbtu each to support its ethane cracker and three polyethylene units, according to updated project documents. The complex’s two gas-phase polyethylene manufacturing lines each will be equipped to produce 550,000 tpy of either HDPE or LLDPE-grade pellets, while a third manufacturing line outfitted with INEOS AG’s slurry loop reactor polyethylene technology will produce 500,000 tpy of HDPE pellets. Alongside installations for steam generation, storage, logistics, cooling water, and wastewater treatment, the complex also will house a 250-Mw cogeneration power unit.
Shell, which in July 2020 completed divestment of its Appalachia oil and gas production assets—including 443,000 net leasehold acres across Pennsylvania with 358 producing wells in the Marcellus and Utica shale formations, as well as all owned and operated midstream infrastructure—has yet to reveal details regarding any supply agreements with regional gas operators for ethane volumes required to feed the Monaca cracker project (OGJ Online, May 5, 2020).
At the US Gulf Coast (USGC), construction rebounded quickly on Saudi Arabian Basic Industries Corp. (SABIC) and ExxonMobil Corp. joint-venture Gulf Coast Growth Ventures LLC’s (GCGV) 1.8-million tpy ethane cracking complex in Portland, San Patricio County, Tex., near Corpus Christi (OGJ Online, Sept. 16, 2019). While SABIC said in its 2020 annual report to investors issued in early 2021 that it expected the project to reach mechanical completion in third-quarter 2022, Paul Fritsch—GCGV’s plant manager—confirmed via broadcast interviews with local news stations in mid-June the complex was about 95% completed and already in the process of starting up utilities at the site for planned commissioning of remaining units during fourth-quarter 2021.
Announcement of GCGV’s expedited startup schedule follows ExxonMobil’s confirmation in its third-quarter 2020 earnings presentation, that the Corpus Christi cracker was under budget and ahead of schedule. Jack P. Williams, the company’s senior vice-president, said in the late-October quarterly earnings call that the GCGV project was benefiting from a more favorable cost environment, as well as ExxonMobil’s implementation of cost-cutting efficiencies and its establishment of a dedicated global projects division ahead of the COVID-19 pandemic.
Formed in 2018 to take advantage of the USGC’s existing infrastructure to capture competitive pricing for US natural gas feedstock and access to rising demand for ethylene-based products in overseas export markets, the 50-50 GCGV JV’s ethane steam-cracking complex will include a 1.1 million-tpy monoethylene glycol (MEG) unit and two polyethylene units with combined capacity of 1.3 million tpy (OGJ Online, July 26, 2022).
In March, Borealis AG said weakening regional polyolefin sales prices at the USGC during first-half 2020 caused by the pandemic resulted in major deviations in construction of an integrated ethane steam cracker and polyethylene plant project in Texas that will be operated by Bayport Polymers LLC (Baystar), Borealis’ 50-50 JV with TotalEnergies Petrochemicals & Refining USA Inc. (OGJ Online, Mar. 1, 2019).
Originally scheduled for commissioning in 2021, the Baystar polyethylene plant under construction at the operator’s existing production site in Pasadena, Tex., is now slated for mechanical completion later this year for targeted startup in first-quarter 2022 (Fig. 2). Once operable, the plant will use Borealis’ proprietary Borstar PE process to produce 625,000 tpy of HDPE. Most recently due to complete construction at TotalEnergies Petrochemical & Refining USA’s 200,000-b/d integrated refining complex in Port Arthur, Tex., by midyear 2021, Baystar’s grassroots 1-million tpy ethane steam cracker is currently scheduled for commissioning by yearend or early 2022, roughly a year behind its originally planned late-2020 startup, according to TotalEnergies and Borealis.
First announced in 2018 and designed to take advantage of abundantly available and competitively priced US ethane supplies, the Baystar cracker will deliver its ethylene production as feedstock for the nearby HDPE plant.
After slowing construction in late-March 2020 to ensure worksite safety and preserve liquidity during the pandemic, LyondellBasell Industries NV told investors in mid-May 2021 mechanical completion of its USGC propylene oxide (PO) and tertiary butyl alcohol (TBA) plant has been delayed to fourth-quarter 2022, about a year later than originally estimated (Fig. 3).
Located on 140 acres at LyondellBasell’s Houston-area complex in Channelview, Tex., the PO-TBA project—which completed first-phase construction in late 2019 and is now due for startup in 2023— will produce 470,000 tpy of PO and 1 million tpy of TBA, the latter of which will move to an associated 34-acre ethers unit to be built at the company’s Bayport complex near Pasadena for conversion into high-octane gasoline components methyl tertiary butyl ether and ethyl tertiary butyl ether (OGJ Online, Mar. 31, 2020).
LyondellBasell said higher costs arising from COVID-19-related delays likely would result in additional civil construction and increased tariffs on materials for the PO-TBA project that could add about 40-50% to the plant’s original $2.4-billion estimated cost.
Ongoing project delays
During the first-half 2021 recovery period, US petrochemical operators were quick to restart projects in advanced stages of construction ahead of the COVID-19 health crisis. Previously announced projects still in preliminary phases of development, however, remained in limbo by midyear.
While project proponents refrained from definitively cancelling plans to add fresh domestic capacity, apprehensions continued to mount regarding impacts near-term capacity expansions in the US and Asia Pacific might have on demand for and availability of domestically produced ethane feedstock supplies. In its most recent Short Term Energy Outlook for July 2021, the US Energy Information Administration (EIA) forecasted that by fourth-quarter 2022 domestic ethane production would average 2.58 million b/d, with ethane demand from US petrochemical producers averaging 2.09 million b/d. During that same period, rising demand for US ethane production from chemical producers abroad—particularly in China, which plans to add roughly 22 million tpy of production capacity (cracking, propane dehydrogenation) between 2021-22—will increase ethane exports to more than 450,000 b/d, leaving less than 50,000 b/d of spare ethane volumes for consumption by US
operators. Alongside threats of increased competition resulting from steadily rising global production capacities in the Asia Pacific, US operators also were cautious of future disruptions
COVID-19 variants could have on an already slowly recovering economy, posing yet another risk to new project development.
After entering an agreement in July 2019 to jointly develop a new $8-billion USGC petrochemical plant, Chevron Phillips Chemical Co. LLC (CPChem)—a joint venture of Chevron Corp. and Phillips 66—and Qatar Petroleum (QP) in April 2021 deferred final investment decision (FID) on the project until 2022 from 2021. In its April quarterly earnings call with investors, Greg Garland, Phillips 66’s chairman and chief executive officer, said the delayed FID resulted from the partners’ joint decision to further monitor economic developments before committing to the project.
To be known as USGC II and originally planned for commissioning in 2024, the complex—if approved—will include a 2-million tpy ethylene cracker and two 1-million tpy HDPE units somewhere along the USGC due to the region’s direct access to abundant Permian basin NGL reserves. CP Chem and QP would own 51% and 49%, respectively.
PTTGC America LLC (PTTGCA), the US subsidiary of Thailand’s GC (formerly PTT Global Chemical), said in a Dec. 30, 2020, release that it has indefinitely delayed FID on its proposed 1.5-million tpy ethane cracker and petrochemical complex planned for Mead Township along the Ohio River in Shadyside, Belmont County, Ohio (OGJ Online, Sept. 24, 2020). While the operator said uncertainty caused by the COVID-19 pandemic prompted the decision to stall the project—most recently due for FID by midyear 2021—local media reports out of Thailand cite GC company officials expressing concern regarding additional obstacles that could drastically alter project economics, including potentially oversupplied markets for ethylene and polyethylene, heightened climate-related regulations, and most importantly, rapidly rising construction costs.
In its 2020 annual report published in March 2021, GC said capital costs of PTTGCA’s petrochemical complex—originally budgeted at about $10 billion—stood at $20.84 billion by yearend. The cost escalation followed withdrawal of Daelim Industrial Co. Ltd. subsidiary Daelim Chemical USA LLC as a project equity partner in mid-July 2020 because of deteriorating market conditions caused by the pandemic and its impact on oil price volatility. While PTTGCA has since insisted it continues to seek a new partner for the proposed development, updates regarding future partnerships have yet to emerge.
According to a final air pollution permit-to-install issued in December 2018 by the Ohio Environmental Protection Agency, PTTGCA’s Belmont complex, if realized, would include six ethane-cracking furnaces and be equipped to produce ethylene, HDPE, and LLDPE using the following units and capacities:
- Ethylene plant, 1.5 million tpy.
- HDPE Unit 1, 350,000 tpy.
- HDPE Unit 2, 350,000 tpy.
- LLDPE-HDPE Unit 1, 450,000 tpy.
- LLDPE-HDPE Unit 2, 450,000 tpy.
Startups, new projects
Despite problems and uncertainties posed by COVID-19 restrictions during second-half 2020 and first-half 2021, US chemical operators did manage to add fresh capacity and advance new projects.
After a yearlong commissioning process interrupted by August 2020’s Hurricane Laura, Sasol Ltd. achieved full operation of its Lake Charles Chemicals Project (LCCP)—an integrated ethane cracker and downstream derivatives complex in Westlake, La., near Lake Charles—in mid-November 2020 with startup of the site’s LDPE unit, the project’s seventh and final (Fig. 4) (OGJ Online, Nov. 16, 2020).
Equipped with processing technology from ExxonMobil, the 420,000-toy LDPE unit—which was damaged in a fire during initial commissioning in January 2020—is one of three LCCP units included in Sasol’s recent $2-billion partnership with LyondellBasell, under which LyondellBasell acquired 50% interest and operatorship of LCCP’s 1.54-million tpy ethane cracker, 471,000-tpy LLDPE unit, LDPE unit, and associated infrastructure (OGJ Online, Oct. 19, 2020). As part of the JV with LyondellBasell—which operates under the name Louisiana Integrated PolyEthylene JV LLC—Sasol retains full ownership and operational control of its Lake Charles Research and Development complex, the 460,000-tpy Lake Charles East Plant ethane cracker and US performance chemicals business assets in Lake Charles—which produce Ziegler alcohols and alumina, ethoxylates, Guerbet alcohols, paraffins, comonomers, linear alkyl benzene, ethylene oxide, and ethylene glycol—as well as access to competitively priced on-site ethylene.
While US petrochemical producers largely loomed on the sidelines during early 2021, plans for new investments in domestic operations finally surfaced by midyear.
In late June, CPChem let a contract to S&B Engineers and Constructors Ltd. to deliver engineering and construction on a grassroots on-purpose 1-hexene plant near the operator’s Sweeny petrochemical complex in Old Ocean, Tex. (Fig. 5) (OGJ Online, June 22, 2021). To be equipped with CPChem’s proprietary technology, the proposed unit will use a feedstock of ethylene to produce 266,000 tpy of high-purity, comonomer-grade 1-hexene, a critical component used in producing polyethylene. Scheduled for startup in 2023, the planned Old Ocean 1-hexene project will join CPChem’s operation of the world’s largest on-purpose 1-hexene plant at the Cedar Bayou chemical complex in Baytown, Tex., to give CPChem a total US 1-hexene capacity of 650,000 tpy.
CPChem also is undertaking a series of approved optimization and debottlenecking projects at its Cedar Bayou complex, JV partner Phillips 66’s Garland told investors in late April. While neither CPChem, Chevron, nor Phillips 66 have officially confirmed details regarding the projects, Garland said the activities are aimed at increasing ethylene and polyethylene production at the Baytown site (Fig. 6).
According to the latest operating data available from Phillips 66, CPChem’s Cedar Bayou complex produces 2.56 million tpy of ethylene, 280,000 tpy of HDPE, and 220,000 tpy of HDPE.
Elsewhere on the USGC, LACC LLC—a venture of Lotte Chemical Corp. subsidiary Lotte Chemical USA Corp. and Westlake Chemical Corp.—let a contract to McDermott International Ltd. in mid-July to provide engineering, procurement, and construction of a seventh heater at LACC’s 1-million tpy ethane cracking complex in Westlake, La. (OGJ Online, July 15, 2021). Scheduled for commissioning during fall 2023, the new heater will be equipped with Lummus Technology LLC’s proprietary Short Residence Time (SRT)-III technology to support cracker operations at the site, according to McDermott.
While new cracking furnaces typically are added to cracker operations to accommodate increased capacity, neither Lotte Chemical nor Westlake Chemical to date have indicated any official plans to expand production at the $3.1-billion Westlake complex, which—commissioned in 2019—produces 2.2 billion lb/year of ethylene and also houses a 700,000-tpy MEG plant operated by Lotte subsidiary Lotte Chemical Louisiana LLC (OGJ Online, May 10, 2019).
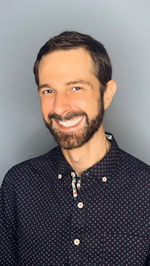
Robert Brelsford | Downstream Editor
Robert Brelsford joined Oil & Gas Journal in October 2013 as downstream technology editor after 8 years as a crude oil price and news reporter on spot crude transactions at the US Gulf Coast, West Coast, Canadian, and Latin American markets. He holds a BA (2000) in English from Rice University and an MS (2003) in education and social policy from Northwestern University.