Flint Hills completes major upgrades at Pine Bend refinery
Flint Hills Resources Pine Bend LLC, a subsidiary of Flint Hills Resources LLC (FHR), Wichita, Kan., has completed a collection of more than $400-million worth of projects designed to increase energy efficiency, reduce air emissions, and improve processing capabilities at its 332,000-b/d Pine Bend refinery in the city of Rosemount, Dakota County, Minn. (OGJ Online, Oct. 10, 2016).
All completed this year, the new technology and efficiency improvement projects—referred to collectively as the Pine Bend Innovations and Technology and Efficiency Improvement Projects (ITEIP)—include one of the world’s largest applications of a technology that converts a traditional source of air pollution into fertilizer, a state-of-the-art combined heat and power system that satisfies much of the refinery’s power needs, and more efficient heating elements that improve production while lowering emissions, FHR said.
Alongside helping to increase production capabilities at the site, the projects are also anticipated to further improve Pine Bend’s operating efficiency, which is already in the top first quartile of all US refineries, according to the operator.
“These projects help continue a 20-year trend of lowering key emissions, a relentless focus on safety and a constant desire to improve the efficiency of our operations,” said Geoff Glasrud, vice-president and manufacturing manager for the FHR Pine Bend refinery.
“We are thrilled to get these projects up and running as we continue to find new and innovative ways to produce the fuels and other products people need while minimizing our emissions and protecting the environment,” Glasrud said.
Since 1997, the Pine Bend refinery has lowered emissions of traditional criteria pollutants by about 70%, while increasing production to help meet demand for transportation fuels. The refinery also has reduced total on-site emissions in 11 of the last 15 years, and its emissions per barrel are about 20% lower than other US refineries, the operator said.
In the past 5 years, Pine Bend has improved its energy efficiency by 10%, advancing it into the first quartile of all US refineries, FHR said, adding that it expects the refinery’s efficiency and environmental performance to continue improving as a result of these newly completed projects.
In addition to supplying most of the transportation fuels used in Minnesota and a large portion of fuels used throughout the Upper Midwest, the FHR Pine Bend refinery also produces asphalt, home heating fuels, as well as raw materials used in a wide range of manufacturing processes, including fertilizers, pharmaceuticals, and plastics.
ITEIP overview
Specifically, the recently completed ITEIP included the following projects:
- Ammonium thiosulfate (ATS) technology and distribution terminal. Pine Bend’s new ATS technology and distribution terminal allows the refinery to convert a traditional source of air pollution from motor fuels (sulfur) into a valuable fertilizer product benefiting farmers and the environment. One of the largest applications of ATS technology in the world, this system also helps the refinery produce ultralow-sulfur gasoline, which lowers vehicle emissions. The refinery said it expects to produce about 100,000 short tons of ATS annually. A new rail and truck distribution terminal near the refinery in Rosemount also will allow ATS to be supplied to farmers throughout the Corn Belt and Northern Plains.
- Combined heat and power (CHP) system. Among Minnesota’s most efficient sources of electric energy generation, the refinery’s new CHP system is providing about 50 Mw of electricity, or roughly 40% of what is required to power the refinery’s operations. The cogeneration of electricity and steam is more efficient than producing them separately, and on-site electricity generation avoids losses associated with transmission and distribution. The Pine Bend CHP uses a combination of a state-of-the-art natural gas combustion turbine, a combustion turbine waste-heat recovery system, and a steam turbine energy recovery system. FHR said it expects Pine Bend’s use of an air-cooled condenser technology to save about 400,000 gal/day of water compared to traditional water-based cooling systems.
- New heaters, improved heating elements. FHR said it expects recently installed new and more efficient heating elements to lower the refinery’s overall NOx emissions by nearly 150 tonnes/year, or 13%. The replacement of two 1950s-era heaters—and the refinery’s largest single source of heater NOx emissions—with new, state-of-the-art heaters help convert a less valued asphalt-like material to gasoline and diesel fuel to help better meet demand for these products. The new heaters are slated on their own to reduce NOx emissions by 50 tpy, which is an 80% improvement over the original heaters. The application of selective catalytic reduction technology to other refinery heating elements further reduces NOx emissions by an estimated 80 tpy. Installation of new burner technologies reduces NOx emissions by an additional 15 tpy.
- Modernized cooling towers. Two modernized cooling towers allow the refinery to better and more efficiently control the need to rapidly heat and cool product. FHR said it expects these improvements to save more than 15 million gal/year of water and reduce energy consumption by at least 10%.
- New gasoil fractionator. A new 670,000-lb gasoil fractionator, built in Cambridge, Minn., and transported 60 miles to Pine Bend, will improve the refinery’s diesel fuel production. The fractionator allows Pine Bend to more efficiently convert less useful gas oil material to diesel fuel to meet consumer demand.
- Wescott propane storage terminal. FHR recently acquired and upgraded a propane storage terminal (previously owned by Xcel Energy Inc.) located in Inver Grove Heights, Minn., to more efficiently manage propane inventories, especially during the winter months when demand is highest.
- Inver Grove Heights storage tanks. FHR also acquired and upgraded storage tanks in Inver Grove Heights previously owned by Xcel Energy. The project helps the refinery more efficiently manage product inventories, especially during maintenance events, so it can continue meeting demand even when operating at reduced capacity.
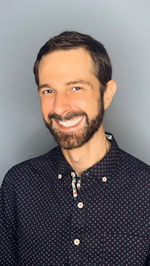
Robert Brelsford | Downstream Editor
Robert Brelsford joined Oil & Gas Journal in October 2013 as downstream technology editor after 8 years as a crude oil price and news reporter on spot crude transactions at the US Gulf Coast, West Coast, Canadian, and Latin American markets. He holds a BA (2000) in English from Rice University and an MS (2003) in education and social policy from Northwestern University.