Repurposing existing oil and gas wells for geothermal applications eliminates drilling costs for new geothermal wells and eliminates plug and abandonment (P&A) costs for decommissioned wells. Drilling represents the most expensive part of geothermal well construction, and decommissioning costs about $20,000 per onshore well with an additional $76,000 for plugging. Repurposing wells also eliminates methane releases from poor or degraded P&A jobs.
To perform economic repurposing, suitable analysis and procedures need to derisk the conversion project. To address these concerns, Texas A&M University performed a study using typical North Sea and European formation properties to model wellbore heat transfer in a converted decommissioned oil well. The study estimated heat production and reinjection of fluid to the reservoir.
A second study by investigators from Curtin University Malaysia, Renewables Consulting Sarawak, Heriot-Watt University, and Universiti Teknologi Petronas investigated geothermal electricity generation from onshore oil and gas wells in high-temperature gradient regions of Baram basin, Sarawak. Simulation models and field data estimated water injection and hot water production from the reservoir. The results showed a linear increase in energy production with original reservoir temperature until 100° C., with non-linear increase above this temperature.
Texas A&M repurposing analysis
Texas A&M performed a numerical study using the homogeneous oil and gas reservoir parameters in Table 1 across the entire reservoir volume. A commercial thermal reservoir simulator evaluated effects of rock properties on water circulation and heat production in a two well injector-producer scenario. A commercial wellbore -modeling tool evaluated effects of casing design, cement type, and annular space on heat generation. Injector and producer were separated by 3,500 ft.
Sensitivity analysis determined effects of the parameters listed in Table 2 on geothermal performance. Simulations were run sequentially with 22 simulations for each parameter for a total of 88 simulations. Simulation rankings were based on the average injection pressure and produced temperature under constant 22,000 b/d injection rate. The forecast covered 30-years of injection and production, and estimated power used a 15% Organic Rankine Cycle (ORC) efficiency ratio.
The injection well is 10,000 ft deep and has a 6-in. internal diameter. Surface temperature is 50° F. and bottom-hole temperature is 250° F., resulting in a geothermal gradient of 2° F./100 ft. Wellbore heat-loss was modeled using a commercial simulator. Heat-transfer coefficient came from published sources. Heat losses along the wellbore were determined by varying the number of casings and total casing depth. Rates were varied to quantify heat losses under different residence times.
Figs. 1 and 2 show reservoir property dependence on thermal power and fluid injection pressure, respectively. Fig. 1 shows that reservoir temperature (TR) and thickness (h) were the major contributors to system performance. Porosity (f), water injection temperature (Tw), and reservoir permeability (kh) had no discernable effect on heat production. TR determines maximum recoverable temperature and h determines thermal breakthrough time (system longevity). A thicker reservoir retards thermal breakthrough, providing longer heat production.
For the fluid injection in Fig. 2, permeability and thickness dictated the pressure required to inject and circulate water underground (wellbore friction was neglected in the analysis). Thicker reservoirs with higher permeability have more injectivity, therefore thickness both slows down thermal breakthrough and allows higher injection rates and subsequently higher energy production.
Fig. 3 shows thermal energy recovery under variations in kh and h. Thicker reservoirs have a high energy recovery ratio and provide good candidates for geothermal retrofitting. Thin reservoirs limit circulation rates. Even under high permeability, heat exchange is too limited to provide good energy ratios. The most important reservoir parameters for providing effective heat production are reservoir temperature, thickness, and permeability, in that order.
With respect to casing design, wells with a higher number of casings have better heat conservation due to low fluid residence time in the wellbore. Increasing rate reduces the advantage of multiple casings by reducing overall residence time, and it is recommended to flow wells at as high a velocity as practical. Larger casings are therefore not optimal in wells which cannot deliver high rates. In these cases, high velocity instead of rate keeps wellbore fluids from cooling during residence.
Table 3 summarizes the importance of each parameter in power production, both with respect to reservoir parameters and casing schemes.
Baram basin
Sarawak’s onshore Baram basin contains high temperature gradients which should make ideal heat sources for geothermal repurposing. There are uncertainties, however, in key parameters required for the technical feasibility of geothermal energy in the basin. Investigators from Curtin University Malaysia, Renewables Consulting Sarawak, Heriot-Watt University, and Universiti Teknologi Petronas examined three specific fields in the basin to determine their estimated power-generation capacity for a minimum period of 30 years. Screening economics of conversion were compared against a baseline levelized cost of electricity (LCoE) for other power generation technologies provided by Sarawak State Energy Co.
The study began by determining the maximum amount of energy that one well can generate in three locations (Fig. 4):
- Asam Paya field. The field is currently producing, but it has low geothermal gradient.
- Adong Kecil West field. The field is currently under appraisal but has an unknown geothermal gradient.
- Engkabang West field. The field has an abandoned exploration well and a high geothermal gradient.
A reservoir simulator estimated the likely range in geothermal heat energy output using input data from publicly available analogue data for surface and downhole parameters from existing fields, recent explorations, and appraisal activities. Most data came from North Perth basin.
North Perth basin provided an analogue for Engkanang as they have nearly identical geothermal gradients (3.6 vs. 3.5° C./100 m, respectively). These gradients are sufficient to generate electricity. As with the Texas A&M study, realistic reservoir and wellbore heat flow properties based on geothermal gradients are required for accurate geothermal evaluations. Development concepts integrated petrophysical and thermal parameters to calculate enthalpy flows from various well configurations. The study included a standard 20° C. heat loss from the perforation point to the surface, and this loss was included in the economic analysis.
Fig. 6 shows GETEM LCoE estimates for power generation. For Engkabang, assuming a BHT of 170° C. at 4,090-m TVD, LCoE is about $0.15 for a 15 Mw plant. This BHT was verbally reported for the field, and data suggests that areas may be as high as 203° C. For the higher temperature, the plant can be upscaled to 30 Mw and GETEM estimates lower values for LCoE. Other estimator tools produced similar LCoE values for Engkabang, and a theoretical Engkabang Deep well with 243° C. BHT and 6,000-m TD resulted in a 60-Mw plant and $0.0745 LCoE. These LCoE estimates bracket the $0.08 benchmark for power generation in Malaysia, and a 30-Mw geothermal power plant is economically feasible.
Using a similar process, Asam Paya field failed as a candidate for large scale electricity generation. The field could, however, produce small-scale cogeneration of electricity to reduce or replace fuel gas currently powering separators and export pumps and provide direct heat for local timber and agriculture industries along the Baram River. Adong Kecil West development, whether for large-scale power generation or local heat production, is indeterminant and hinges on geothermal gradient maps derived by further research.
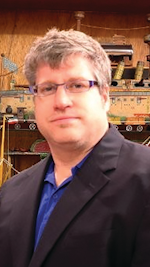
Alex Procyk | Upstream Editor
Alex Procyk is Upstream Editor at Oil & Gas Journal. He has also served as a principal technical professional at Halliburton and as a completion engineer at ConocoPhillips. He holds a BS in chemistry (1987) from Kent State University and a PhD in chemistry (1992) from Carnegie Mellon University. He is a member of the Society of Petroleum Engineers (SPE).