Surfactant EOR increases Permian oil recovery
Unconventional reservoirs typically yield less than 10% oil recovery. In the Permian basin, enhanced oil recovery (EOR) schemes include CO2 injection, huff and puff, water injection, and, to a lesser extent, surfactant injection. These secondary recovery methods have met with mixed success, with CO2 injection suffering from poor sweep and premature breakthrough, and water flooding limited by oil-wet reservoirs which prevent spontaneous water imbibition into the fractures to displace residual oil.1
Surfactant injection into oil reservoirs increases crude recovery by changing wettability of the reservoir and reducing interfacial surface tension (IFT) between crude and water. This reduction decreases capillary pressure and mobilizes fluids out of the propped fracture networks. To work, surfactants must adsorb on the surface of the rock.
Surfactant EOR
Most Midland basin and Permian basin shale reservoirs are oil-wet or intermediate-wet. Capillary pressure has a negative value in oil-wet reservoirs due to high water-drop contact angle (q) on the hydrophobic rock surface, and water cannot imbibe into the fractures (Fig. 1). Residual oil in large fractures is essentially trapped, and significant oil is trapped within microfractures. Surfactants displace oil and increase recovery by changing the wetting phase of the rock. This reduces capillary pressure and increases imbibition. The Young-Laplace equation (See equation) shows how reducing IFT (s) decreases capillary pressure and reducing q below 90° drives water imbibition into a pore of radius r. The same effect holds true for microfractures.
In addition to forcing oil out through water imbibition, surfactants shift relative permeability curves through decreases in oil droplet sizes in the oil-continuous phase by reducing IFT. Fig. 2 shows the effects of a surfactant on core relative permeability.2 Baseline relative permeability to oil (kro) was 20% (0.2 fraction) in a Wolfcamp core-sample containing 10% pore-volume fraction of distilled water and 90% oil-volume compared with oil permeability in a 100% oil-saturated core. Addition of surfactant, however, increased oil relative permeability to 60%. Throughout the 0.9 to 0.1 water-saturation range, relative oil permeability improved with addition of surfactant. Oil drainage tests showed that cumulative oil recovery from the core improved with addition of these surfactants in proportion with their improvement on kro.
Surfactants are therefore used as additives in fracturing fluids for unconventional oil and gas completions to reduce water retention and water blockage. They are also used as post-treatments for existing wells in either single treatments or cyclic treatments analogous to huff-and-puff cyclic gas injection. In all cases, the surfactant’s ability to lower IFT and change wettability of reservoir rock is critical to improving oil recovery.
Permian EOR
Three surfactant packages were tested for EOR in a Permian application by mixing surfactant with slickwater and a high-viscosity friction reducer in the fracture treatment.3 One surfactant is a blend of nonionic alcohol ethoxylate surfactants, one is a microemulsion additive, and one is a proprietary synthetic surfactant system (novel).
With well shut-in expected for up to a month before production, long-term surfactant stability was tested at elevated temperature and pressure. The surfactants were mixed into 2% (by weight) KCl brines at a 2 gal concentrated surfactant solution/thousand gal brine (gpt) concentration. Solutions aged at 150° C. and 200 psi, and surface tension was periodically measured over a 45-day period using the Wilhelmy plate method. Surface tension is reported in units of milliNewton/m (mN/m).
Fig. 3 shows that the novel surfactant maintained stability for about 18 days, with slight continual degradation (expressed as an increase in surface tension) to the end of the test period. The microemulsion was also stable over the test period, albeit at higher overall surface tension for the same surfactant package concentration (the actual molecular concentration of surfactant in solution was not revealed in the study). The nonionic blend initially yielded low surface tension, comparable to the novel surfactant, but it started to significantly degrade after about 15 days.
Interfacial tension between brines and oil was evaluated with a spinning drop tensiometer. Brines were prepared with total dissolved solids (TDS) of 20,000-270,000 ppm, covering typical ranges of connate water in Permian wells. Surfactant was introduced into the brines at 1 gpt, and a small drop of crude oil was injected into a capillary tube containing the surfactant-brine solution at 90° C. The oil-drop diameter was imaged by a camera while the capillary tube was spinning in the chamber. IFT was calculated based on drop shape and phase densities. Fig. 4 shows that the novel surfactant was stable in all tested brine-TDS concentrations and yielded about 10% IFT of the nonionic surfactant. The ethoxylated groups in the nonionic surfactant started to dehydrate at higher salinities, resulting in a less water-soluble and subsequently less effective surfactant.
Oil drainage from aqueous phase displacement tests simulated gravitational- and capillary- dominant flow conditions in the presence of surfactant. Tests included fracturing fluids made with surfactant in friction reducers and in linear gels with ammonia persulfate (APS) breakers (see Table).
A sand pack column of 100-mesh white sand (30 g) was saturated with the test fluids prepared in a 2:1 (by weight) ratio of freshwater fracturing-fluid:Permian brine. Excess fluid remained above the sand pack during equilibration. Sand pack temperature was held at 65° C., and the sand was sonicated to compact the column. After equilibration, excess brine drained through a bottom valve until brine was level with the sand pack surface. The drainage valve was shut, and 20 ml crude oil was poured on top of the column. The system was brought back to temperature, and breaker-containing fluids were shut in to break overnight. When ready, fluid drainage was measured over time after opening the valve.
Fig. 5 shows oil drainage through core exposed to Fluid 1 containing surfactant and friction reducers. The novel surfactant produced the fastest oil breakthrough time, with lowest water saturation (saturation data not shown). The microemulsion performed second best in this test, and these relative rankings held for all fluid systems except for Fluid 3, in which the microemulsion performed worst. In all cases, including high-salinity brines, the novel surfactant had superior oil drainage.
Upton County field application
The novel surfactant system was evaluated against a microemulsion in the Permian basin Wolfcamp play, Upton County, Tex.. Like Fluid 1 in the test program, the surfactants were incorporated in fracture fluids containing slickwater and a high-viscosity friction reducer (HVFR). Five wells were completed with the novel surfactant and initial production was compared with six wells which were similarly completed with fluids containing microemulsion surfactant. Production data were from Rystad Energy Co., converted to boe using 21-MMscfd gas/1-bbl oil conversion factor.
Fig. 6 shows average cumulative production for wells normalized by lateral footage. The novel surfactant improved oil equivalent recovery at 30- and 90-days initial production compared with microemulsion-containing fluids. Similar results were observed if normalized by volume of fracture fluid pumped or amount of proppant placed. Jobs comparing surfactants in a hybrid slickwater-linear gel system (without HVFR) yielded similar results.
Biosurfactants
Microbial surfactants are a class of amphiphilic molecules produced by yeasts, bacteria, and fungi using carbohydrates and organic oils as a carbon source. Biosurfactants are classified based on chemical structure and origin. The hydrophilic head is usually an aminoacid, peptide mono-, di- or polysaccharide, and the hydrophobic tail is usually saturated, unsaturated, linear, branched, or hydroxylated fatty acid.4
A non-genetically modified organism (GMO) microbial biosurfactant (BSF) has been developed with binary and ternary mixtures of Sophorolipid glycolipid in a bioreactor process to produce surfactant in sufficient quantities and cost for oilfield applications. The BSF contains micelles about 3.1 nm in size, as much as 30 times smaller than typical synthetic surfactant molecules and three times smaller than nanofluids. It is stable up to 300° F. and compatible in fluids with 2-10 pH. BSF does not contain live microbes (no biofouling). Surfactant stability has been reported in brine up to 150,000-ppm TDS.
About 2-ppm minimum surfactant concentration is required to reduce IFT between hydrocarbons and water as measured using a drop shape analysis instrument and the pendant drop method at ambient temperature (Fig. 7). This concentration produces a gradual reduction in IFT, eventually decreasing IFT to 30 mN/m during the 900-sec test period. Additional surfactant, however, results in rapid IFT reduction, with 30 ppm surfactant dropping IFT to below 20 mN/m within 200 sec.
BSF adsorbs onto calcite, silica, alumina, carbonate, and kaolinate. Fig. 8 shows BSF adsorption on minerals sieved to 200 mesh (75mm). Adsorption is highest on kaolinite, calcite, and carbonate, at around 200 ppm surfactant per gram of mineral over a 24-hr exposure period. This adsorption is roughly 50% of surfactant in the initial solution. Adsorption is rapid for kaolinite, and slightly slower for calcite.
BSF surfactant retention is higher than typical synthetic surfactants. Wilson et. al studied a series of five alcohol-derived surfactants with differences in branching types and degrees. Compared with BSF, conventional surfactants adsorbed 1-8% on Berea and 9-19% on limestone at the end of 13-day exposure to rock samples.5
Once adsorbed, BSF change surface wettability through changes in contact angle, as measured by a drop-shape analysis instrument and calculated from high-resolution frames (Fig. 9). Depending upon concentration, the water-drop contact angle decreases up to 60° on an oil-impregnated core surface with 1-gpt surfactant solution concentration, changing wettability from oil-wet to water-wet and driving brine imbibition.
Delaware basin BSF application
A four-well pad treatment program addressed declining production without performing a full mechanical workover. In contrast to the Wolfcamp play treatment, this application was for EOR, not primary recovery. Each well in the pad had a 5,000-ft lateral in a shale reservoir. A single pumper truck was used to bullhead inject the BSF solution. Fig. 10 shows production decline before treatment and recovery after treatment.
After treatment, both oil and gas volumes were above untreated forecast decline curves, with 40-Mcf incremental gas and 4,500-bbl total incremental oil produced above forecast over about 160 days of production since treatment. Treatment cost was recovered within 4 months and added $240,000 incremental revenue with a 1.6 return on investment with respect to incremental revenue and cost.
References
- Patil, P.D., Rohilla, N., Katiyar, A., Yu, W., Nelson, C., Falcone, S., and Rozowski, P., “Surfactant Based EOR for Tight Oil Unconventional Reservoirs through Wettability Alteration: Novel Surfactant Formulations and Their Efficacy to Induce Spontaneous Imbibition,” URTeC 2896289, Unconventional Resources Technology Conference, Houston, Tex., July 23-25, 2018.
- Zhang, F., Saputra, I.W.R., Parsegov, S.G., Adel, I.A., and Schechter, D.S., “Experimental and Numerical Studies of EOR for the Wolfcamp Formation by Surfactant Enriched Completion Fluid and Multi-Cycle Surfactant Injection,” SPE-194325, SPE Hydraulic Fracturing Technology Conference and Exhibition, The Woodlands, Tex. Feb. 5-7, 2019.
- Do., L., Kazempour, M., Harkness, K., Moradi, M., and Street, J.P., “Developments in Hydrocarbon Production Enhancement Aids Under High Temperature and High Salinity Conditions for Hydraulic Fracturing,” SPE-209946-MS, Unconventionals in the Middle East – From Exploration to Development Optimization held in Manama, Bahrain, Mar. 23-24, 2022.
- Shumway, M., McGonagle, R., Nerris, A., Aguiar, J.I.S., Mahmoudkhani, A., and Jacobs, D.M., “Green Well Stimulation Fluids for Enhanced Oil Recovery from Tight Sand Formation: Field Wide 70+ Wells Study Over 4 Years,” SPE-204370-MS, SPE International Conference on Oilfield Chemistry, The Woodlands, Tex. Dec. 6-7, 2021.
- Wilson, D., Poindexter, L., and Nguyen, T., “Role of Surfactant Structures on Surfactant-Rock Adsorption in Various Rock Types,” SPE-193595-MS, SPE International Conference on Oilfield Chemistry, Galveston, Tex., Apr. 8-9, 2019.
- Shumway, M., McGonagle, R., Nerris, A., Aguiar, J.I.S., Mahmoudkhani, A., and Jacobs, D.M., “Green Well Stimulation Fluids for Enhanced Oil Recovery from Tight Sand Formation: Field Wide 70+ Wells Study Over 4 Years,” SPE-204370-MS, SPE International Conference on Oilfield Chemistry, The Woodlands, Tex. Dec. 6-7, 2021.
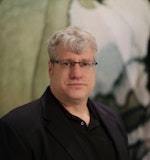
Alex Procyk | Upstream Editor
Alex Procyk is Upstream Editor at Oil & Gas Journal. He has also served as a principal technical professional at Halliburton and as a completion engineer at ConocoPhillips. He holds a BS in chemistry (1987) from Kent State University and a PhD in chemistry (1992) from Carnegie Mellon University. He is a member of the Society of Petroleum Engineers (SPE).