Prolific Paleogene-age Wilcox reservoirs extend from onshore to deepwater offshore Gulf of Mexico (GOM). Discovery wells delineated the play across more than 35,000 sq km, and oil production from ultradeepwater Wilcox reservoirs began in 2010.
The extreme conditions and location of these Wilcox sands, however, have slowed their full commercial development. New technologies will be required for full exploitation of these areas.
To address this issue, Shell PLC designed completion strategies and tools based on onshore multifracture completions to access multiple low-permeability Wilcox lenses in a single completion. A high-angle multi fractured (HAMF) system incorporates typical land-based fracsleeve designs but with a redesign incorporating a sand-control screen and an additional shifting sleeve to comply with offshore environments.
The system was modeled with single-well numerical simulation and full field development, and an offshore trial proved out the system.
Deepwater Wilcox
Wilcox sandstones in deepwater Gulf of Mexico contain large hydrocarbon deposits which can extend production throughout offshore GOM waters. Water depths for these reservoirs exceed 4,000 ft. Ultimate technically recoverable resources from 26 discoveries stand at 22.6 billion boe—the largest reserves of any reservoir in US Federal waters—and the play extends into Mexican territory (Fig. 1).
“The WWS represented a major modification to the basic tool as used on land. Shale or unconventional wells do not experience sand production, but the Wilcox reservoirs are expected to produce sand over the life of the well, especially as depletion increases.”
The deepwater Wilcox formation contains Upper (or Late) Paleocene to Lower (or Early) Eocene age siliciclastic turbidites and is a subunit of the Lower Tertiary system. Onshore deltaic sediments provided the source of the Wilcox with clastic sediments deposited in a slope system producing offshore minibasins and slope fans. The top of Wilcox in Alaminos Canyon is 12,000-20,000 ft TVD below sea level (TVDSS) and 25,000-33,000 ft TVDSS in Keathley Canyon and Walker Ridge.
Due to burial depth, reservoir temperatures can exceed 200° F. Hydrostatic and geopressured mechanisms result in 7,000-29,000 psia reservoir pressures. Reservoir material ranges from fine-grained sand to coarse silt which are moderately-to-poorly sorted, resulting in less than 10 md reservoir permeability.
Wilcox sands exhibit high (2,000-10,000 psi) uniaxial compressive strength (UCS) compared with typical GOM Miocene sands in commercial reservoirs, which have UCS typically less than 750 psi. Wilcox sanding-potential studies indicate low risk for sand production for up to 4,000 psi pressure depletion, in contrast to low-to-zero drawdown thresholds to produce typical GOM Miocene sands. Expected sand production volumes from Wilcox formations, however, are less than Miocene sands under failure conditions. Wilcox reservoirs have minimal compaction expectations, with a 1.3% compaction prediction for a 300 ft net pay interval at 5,000 psi depletion.
Exploitation
Wilcox reservoirs have been exploited by onshore Texas deep gas wells, and the play extends offshore and into areas below and beyond the salt canopy of Alaminos Canyon, Walker Ridge, and other deepwater protraction blocks. BAHA No. 2 well first discovered deepwater Wilcox hydrocarbons. Subsequent discoveries expanded the play updip and downdip, and total estimated acreage stands at more than 35,000 sq km.
Ultradeepwater Wilcox oil production began with the 2010 Great White-Tobago and 2012 Cascade-Chinook developments. Production from Wilcox formations accounted for 16% of US GOM production in 2022 and is estimated to increase to 37% of total GOM production by 2030. Based on the extreme conditions, location, and petrophysical characteristics of the Wilcox sands, full Wilcox commercialization will require new completion technologies.
Typical GOM developments produce from single zones with 100-2,000 md/cP mobilities and 10,000-100,000 md-ft permeability-thicknesses (kxH). Formations are over-pressurized with 8,000-12,000 psi reservoir pressures, resulting in 25-40% recovery factors (RFs). EURs typically are 15-30 million bbl.
Wilcox reservoirs have low mobility (1-40 md/cP) and low permeability (1-20 md). They offset these disadvantages by containing large gross interval lengths, up to 2,000 ft, and high reservoir pressures; but RFs are still lower than typical deepwater completions (Table 1). To make a commercial well, multiple reservoirs must be stacked into one completion to yield sufficient kxH to overcome low mobility. Best estimates are that 2-3 sands at a minimum must be combined to produce a commercial well. These reservoirs are separated by 5-200 ft shale breaks, requiring novel offshore completion tools to combine and stimulate lower-permeability Wilcox sand intervals while isolating shale in a single well.
Single-trip sequential fracturing tools have successfully completed Wilcox wells, but these systems are limited by high cost, low number of stages available, poor tool spacing between sand intervals, limited perforated interval optimization per stage, and low-to-moderate inclination angle restrictions (<50°). These limitations can bypass reserves, and they have been completed only in Wilcox reservoirs at the higher end of the mobility range with a thick hydrocarbon column to match the tool’s geometric limitations.
An ideal completion strategy increases EUR/RF beyond that typically obtained from conventionally completed vertical fractured wells. New techniques and tools, however, cannot significantly increase capital expenditure (capex), and must be compatible with deepwater well construction and production systems. To find a suitable system, Shell performed a screening study by analyzing concepts which had been successfully deployed in reservoirs with similar characteristics to Wilcox sands.
The HAMF completion scheme provided the best option to complete Wilcox sands given the low-mobility formation characteristics and offshore operational constraints. Analog offshore HAMF wells containing 0.1-30 md permeability formations experienced 270% uplift in rate and 30% uplift in EUR over vertical wells. This design also results in higher RFs and drains larger areas compared with conventional vertical multizone systems. By combining multiple sand strata, the system reduces the total number of wells in a field and overall field-development capex.
High-angle wells (>75°) cut across multiple sand intervals, accessing sufficient kxH for economic production. Horizontal wells (90°) through a single lens provide minimal advantages in this environment because most single Wilcox sand packages exhibit insufficient productivity for economic single-zone completions (Fig. 2).
Multifracturing modeling
Analytical and numerical modeling studies evaluated the productivity of deepwater Wilcox HAMF completions. The numerical model evaluated HAMF uplift relative to a vertical fractured well using a simple box model in a commercial 3D reservoir simulator where homogeneous subsurface properties formed elements in a planar reservoir. Low kv/kh values (<0.01) matched typical Paleogene properties and accurately captured layering in low-mobility reservoirs. This approach minimized vertical flow into HAMF completions when the fracture height was less than the gross interval height.
Thin, high permeability streaks modeled transverse fractures within the reservoir. Modeled HAMF fracture height was less than the gross reservoir interval height and vertical well fracture-height equaled the gross thickness. Rate/EUR predictions were performed using -4 skin for the vertical well. Simulations stopped at 500 bo/d, which was considered the minimum economic rate.
After more than 500 simulations studying the effect of various parameters on the initial rate/EUR of a HAMF well vs. a vertical fractured well, the HAMF completions consistently produced higher initial rates, EUR, and RFs, in line with the results from the analog well studies (Fig. 3).
At 2.5 md/cP reservoir mobility, HAMF produced the same cumulative oil as the vertical fractured well in 11 years, vs. 22 years respectively. The differences between the two are directly proportional to reservoir mobility. At high reservoir mobility (25 md/cP) EUR is nearly identical between the completion techniques, with HAMF reaching total cumulative oil about 4 years earlier than the vertical well based on typical deepwater discount rates and the annual operating costs. At low reservoir mobility (0.25 md/cP), EUR is too low to achieve economic recovery indicating that mobility thresholds exist below which no completion will yield positive results.
HAMF field model
Field modeling of a low-mobility reservoir incorporated more realistic conditions than the simple numerical box model, including detailed fracture geometry. The field model represented a typical highly heterogeneous Wilcox reservoir with interbedded shale. The reservoir had 1-50 md/cP mobility, 300-350 ft gross thickness, and 0.01 matrix kv/kh.
The field included a vertical well producing northwest of a fault and a HAMF well producing southeast below the fault. The vertical well had a 330-ft fracture along the entire formation interval, and the HAMF well contained a 2,500-ft completion interval with six fracture treatments. Both wells produced concurrently during the simulations.
Fracture geometries came from a fracture simulator. The simulator predicted vertical well fracture heights spanning about 260 ft of the 330-ft interval and a 330-ft propped fracture length using a 40-bbl/min treatment with 35-lb/Mgal borate crosslinked fluid and about 650,000 lbm of 20/40 ceramic proppant ramped up to 10 ppa. The simulator predicted HAMF fracture heights of about 220 ft and a 250-300 ft fracture length from a 30-bbl/min treatment rate and 400,000 lbm of 20/40 proppant per fracture. Pumping conditions for both wells represented current offshore vessel practices and limitations.
A reservoir model predicted production rates and EUR from these input parameters. The HAMF model assumed 250-ft fracture lengths, 3,000 md-ft conductivity, and 200-ft maximum fracture height for all fractures. Fractures with wellbore initiation points close to bounding shales had smaller heights than those in the middle of the zone. The vertical well model assumed a fracture over the entire 330-ft interval with -4 effective skin.
Fig. 4 shows predicted EUR and rates for the wells. HAMF exhibits 50% more EUR than the vertical well with a six-fold increase in initial rate. It reduced time to abandonment by about 9 years. HAMF EUR and rate uplift also were higher in the field model than a box model simulation using a reservoir with the same average mobility.
A second simulation replaced the HAMF well with a second vertical well. HAMF decreased the EUR from the vertical well compared with dual vertical-well simulation, indicating that HAMF successfully competed with the vertical well for reserves through a larger drained volume, despite being on the other side of a fault. A larger drainage radius allows for wider inter-well spacing and a reduction in the total number of wells needed for development.
HAMF tool design
Table 2 lists the statement of requirements (SORs) for completion equipment and operations derived from the modeled HAMF well design. These SORs were derived from previous hard rock deepwater completions, including experiences with annular isolation and screenout recovery. A system analysis ranked completion systems based on critical parameters with respect to production, drilling, frac design, completion and installation time and cost, and well intervention capabilities, including selective stimulation and isolation.
Based on this analysis, a dual-barrel frac sleeve with wire wrapped screen (WWS) liner inserts for solids control and a sliding screen to isolate frac ports was chosen, given the basic tool’s extensive land run-history and recent installations in shallow-water multiple horizontal fractured wells (Fig. 5). It has a proven cementing capability, can be easily modified, and is straightforward to deploy and set. The sleeves provide a full-bore ID and selective isolation for future interventions, which is a critical contingency for deepwater wells.
The WWS represented a major modification to the basic tool as used on land. Shale or unconventional wells do not experience sand production, but the Wilcox reservoirs are expected to produce sand over the life of the well, especially as depletion increases. Slotted liners were originally specified but expected drawdown and plugging risks exceeded slotted liner capabilities. The qualified WWS design passed erosion, burst, and collapse tests.
An additional modification included adding a dual-barrel sleeve to the original single-barrel system. A lower barrel opens and closes frac ports and the upper barrel shifts the WWS across the frac port for production. The dual barrel design resulted from a failure modes, effects, and criticality analysis (FMECA) on the single-barrel sleeve design. The dual design reduces the risk of inadvertent functioning of the sleeve under subsea conditions, and it can open and close the frac sleeve multiple times in case of operational delays.
Flow paths and frac ports were redesigned from standard land-based systems to increase erosion resistance. Increases in port area decrease velocity through the tool, and a redesigned frac wedge more smoothly redirects flow through the ports.
Additional tool upgrades included improving the axial rating to 150,000 lb from 80,000 lb and improving erosion resistance. The redesigned system underwent pressure, temperature, and erosion testing to derisk it for deepwater deployment.
HAMF tool operation
The HAMF design handles multiple stages to custom-space fracture treatments. Initial deployment of the frac sleeve cements the sleeve and production liner in place. Cemented liners are required because uncemented liners in Gulf of Mexico Paleogene sands potentially produce excessive solids which may negatively affect production.
The sleeve is run with the production liner, eliminating additional time and risk of making up and running a post-perforating lower completion system. Neither a perforation run, sump packer, or deburr run are necessary. The system supplies a flush ID through the sleeve and liner for operational flexibility and future intervention work. A coil tubing- or drill pipe-deployed service tool shifts the dual-barrel frac sleeves to open or close frac ports and shifts the WWS in place for production.
A resettable packer on the service tool isolates stages below the frac sleeve. Fig. 6 illustrates the sleeve positions. Shifting the lower barrel down with a fracture isolation assembly (FIA) exposes frac ports for the fracture treatment. Post treatment, the barrel is shifted up to close the ports when the FIA is pulled out of hole (POOH). Running the reopening BHA shifts the upper barrel down to lock the WWS across the closed frac ports. The tool subsequently shifts up the upper barrel to expose the frac ports, and then is POOH. Production flows through the frac port and the screen protects the well from solids intrusion.
An onshore field trial proved the design in a well with an 8,300-ft MD completion zone and 4,000-ft lateral. The system successfully ran and cemented ten sleeves. Seven sleeves opened and were fractured by 25-ppg crosslinked gel with 20/40 proppant via a tapered workstring. A casing leak occurred on Stage 8, and remaining stages were left untreated.
Acoustic imaging logs showed that six sleeves functioned perfectly with screens locked across the frac ports. There was only partial screen coverage on Sleeve 2, and proppant flowed back during production. A relog confirmed proppant through this sleeve. Subsequent lab analysis revealed proppant bypass through a poor internal sleeve tolerance. A redesigned sleeve addressed this failure mechanism.
Bibliography
Oletu, J., Prasad, U., Ghadimipour, A., Sakowski, S., Vassilellis, K., Graham, B. Park, N., and Li, L., “Gulf of Mexico Wilcox Play Property Trend Review,” OTC-24186, Offshore Technology Conference, Houston, Tex., May 6-9, 2013.
Vitthal, S., Goncu, A., Spencer, V., Jackson, I., Xiao, X., Song, C.Y., Vanee, M., and Cheeseman, B., “Development and Qualification of a High Angle Multi-Frac (HAMF) Completion System for Deepwater Subsea Wells,” SPE-220794-MS, SPE Annual Technical Conference and Exhibition, New Orleans, La., Sept. 23-25, 2024.
Vitthal, S., Van Zanten, R., Malbrough, J., Tallin, A., Reynolds, M.A., Dawson, J., and Hoeman, K., “Development and Evaluation Of An Alternative Fluid For Offshore Fracturing Of Moderate To High Permeability Formations,” SPE-220784-MS, SPE-220794-MS, SPE Annual Technical Conference and Exhibition, New Orleans, La., Sept. 23-25, 2024.
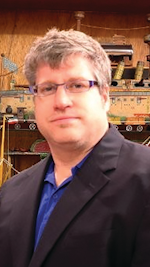
Alex Procyk | Upstream Editor
Alex Procyk is Upstream Editor at Oil & Gas Journal. He has also served as a principal technical professional at Halliburton and as a completion engineer at ConocoPhillips. He holds a BS in chemistry (1987) from Kent State University and a PhD in chemistry (1992) from Carnegie Mellon University. He is a member of the Society of Petroleum Engineers (SPE).